Now's a good time for center pivot maintenance, February 22, 2019
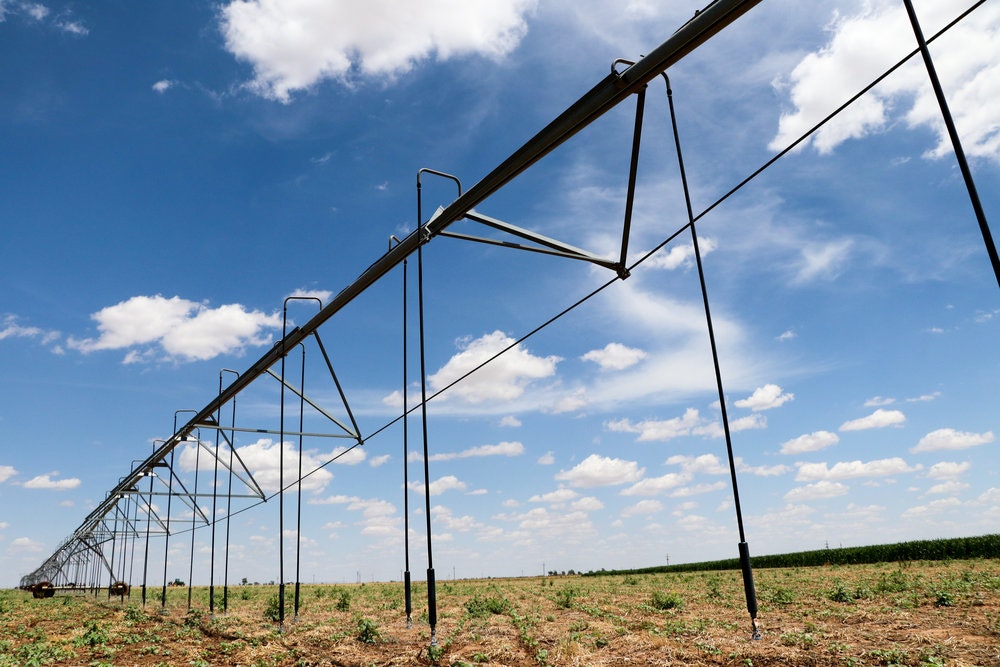
AMARILLO – Spring planting is just around the corner, so for producers with irrigation systems, now is a good time to do some safety maintenance on their pivot systems, according to a Texas A&M AgriLife Extension Service specialist.
In the spring, producers are busy making seed selections and prepping fields, but they also need to remember how important it is to maintain center pivots, said Dr. Kevin Heflin, AgriLife Extension agronomy program specialist, Amarillo.
Annual center pivot maintenance can enhance the efficiency of the irrigation applications as well as the safety of the system, Heflin said. While modern center pivots are safe and essential tools for agriculture production, every year there are accidents and tragedies surrounding these irrigation systems, primarily on the electrical side.
Estimates are there are more than 7,500 center pivot irrigation systems in the Texas High Plains alone, Heflin said. After working with and monitoring many systems over the years, he wants people to know there are some simple things to look for in a safety and maintenance check that can save lives and time once the irrigation season gets underway.
“Some of these systems are older, so it is important to make sure to maintain them and look for potential problem areas,” he said.
Five things to monitor that Heflin discussed are:
– General maintenance issues. Tires, lug nuts, truss rods and brackets, and gear motors are all things that need visual inspections.
“For example, a loose bracket can cause an entire center pivot to fall; a bad tire in the middle of watering can shut down the whole system.”
– Storm damage from wind and lightning.
“Vibrations from strong winds can loosen and fatigue metals. Also, lightning can damage the electrical components, so look for singe marks on electrical panels or a blown transformer on the power pole. Lightning strikes can also damage fuse boxes and cause the metal components to energize and become deadly.”
– Rodent damage in and around electrical boxes.
“Just look for chewed wires that will need to be replaced before the system can be operational. If rats or field mice can find a way into an electrical box, they will often chew the coating off the wires. This could lead to a system malfunction and increase the risk of electrical shock.”
– Improper grounding.
“Make sure the center pivot itself is grounded and the electrical box and transformers are grounded. Safety is primary. The cost of a grounding rod and wire is about $20, pretty cheap to ensure everyone’s safety. We make sure we put them at the pivot control panel and the electrical disconnect boxes. The power company will provide grounding for the transformers supplying the three-phase power.”
– Vandalism, such as the stripping of copper wire from these systems.
“It’s better to go ahead and do the visual and conscious inspection now than to wait until it is time to turn the system on and find the issues.”
Heflin said producers should also ensure electrical boxes are relatively clean and fuses/breakers are properly sized for the voltage and amps being used. He also said it might be good to have a certified electrician inspect the terminal lugs in the electrical boxes to ensure they are tight and making good contact with the wires.
“Also, if you have repairs made to the center pivot or well, go back in and inspect the work,” Heflin said. “We’ve found buried conduit line that was damaged by a contractor and taped up with black tape and reburied without our knowledge. This type of carelessness can lead to an electrical failure, or even worse, a loss of life.”
These routine maintenance and safety inspections do not have to be overly burdensome, he said, and they are worth the time and effort now to prevent breakdowns and tragedies down the road.